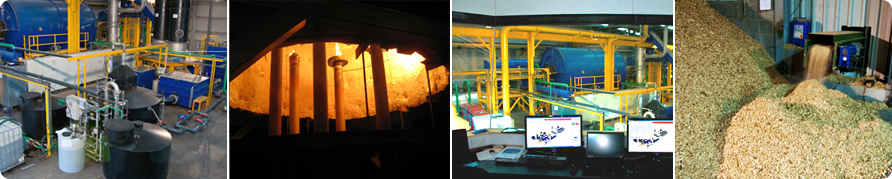
Online Brochure


The global economy has witnessed a combination of a credit-fuelled financial crisis, accelerating climate change, and the looming peak and decline in oil production. Together with these events, global waste management has created challenges for all countries, to be environmentally-responsible, energy efficient, and technologically aware in respect of the processing of waste. The challenges weigh more heavily in particular regions due to the uneconomic scale, uneven spread of waste volumes, and long transportation distances involved. Technology policy lies at the core of these challenges. Global spatial development stresses the need for economic diversification in rural areas through strategies based on local resources.
There is a need for technological solutions that can cope with the constraints of resources availability and, at the same time, be able to decouple growth from environmental degradation. There are vast and immediate opportunities in the Renewable Energy and Energy from Waste sectors which contribute to the achievement of global policy targets and also offer excellent opportunities for decentralised business innovation. Small-scale biomass and waste based energy solutions are able to answer the challenges of resource availability, while progressively reducing the impact of human activities on the environment.
Premier Green Energy owns the exclusive rights to design, build, distribute, and operate advance thermal processing equipment which is fully patented. The technology facilitates the production of sustainable energy combined with an environmentally friendly solution for waste management and resource recovery across small, medium and large scales. The technology works in conjunction with existing waste, energy and recycling infrastructure and does not require excessive capital input.
Brief Profile of Premier Green Energy
PGE is the provider of this leading edge technology to the waste management and biomass sectors. The core activities include build, supply and commissioning of the PRIMA 3000 pyrolysis unit, together with the provision of ancillary equipment including; gas engine(s), heat recovery system(s), gas scrubbing, emissions monitoring system(s), and pre-treatment and fuel transfer mechanism(s). PGE can offer a complete or partial solution to private waste operators, local authorities and large consuming energy industries.
Advanced thermal treatment (ATT) technologies are all those technologies applied to the processing of waste streams and biofuels, whose ultimate objective is energy conversion from waste streams. Fuels can comprise of a multiplicity of waste, including household, industrial, commercial, construction and demolition wastes. It also includes garden and food processing wastes, tyres, chicken litter and many more. Feedstock can, in general, be thought of as all those wastes that would previously have been sent to regulated landfill sites.

In the process illustrated above, the energy content of the fuel feedstock or waste streams is recovered primarily in the form of syngas and heat that can subsequently be utilised for electrical power generation, or utilised for either local or district heating
Three options, as illustrated herewith, are generally available to facilitate the recovery of energy from waste. PGE has chosen the option of pyrolysis as the most appropriate and cost effective technology.

Pyrolysis is a thermal treatment process that uses high temperatures, in the absence of added oxygen, to break down waste during which syngas and a solid char are formed. However, it is still classified as incineration in the European Union (EU)’s Waste Incineration Directive (WID) 2000/76/ EC, and has to meet the mandatory emissions limits that are outlined in that Directive.The general characteristics of pyrolysis of a waste stream are as follows:• Key products are syngas ( whose main combustible components are carbon monoxide, hydrogen, methane and some longer chain hydrocarbons including condensable tars, waxes and oils) and a solid residue char (consisting of non-combustible material and a significant amount of carbon);• The general lack of oxidation, and lack of an added diluting gas, means that the net calorific value (NCV) of syngas from a pyrolysis process is likely to be higher than from a gasification process (provided substantial quantities of carbon are not left in the solid residues). Typical NCV of the gas produced is from 10 to 20 MJ/Nm3.Pyrolysis also offers the potential option of more innovative use of the pyrolysis syngas other than immediate combustion to produce heat. Pyrolysis generally takes place at lower temperatures than for incineration and gasification. The result is less volatilisation of carbon and certain other pollutants such as heavy metals and dioxin precursors into the gaseous stream. Ultimately, the flue gases will need less treatment to meet the emission limits of WID.The solid residues from the pyrolysis process can contain up to 40% carbon representing a significant proportion of the energy from the input waste. Recovery of the energy from this char is therefore critically important for energy efficiency.
The PGE pyrolysis process typically has three stages:• Heating the waste in an oxygen-free atmosphere to produce syngas, oils and char (carbon & ash).• ‘Scrubbing’ or cleaning the syngas to remove some of the particulates, hydrocarbons and soluble matter.• Using the scrubbed syngas to generate electricity and, in some cases, heat (through combined heat and power – CHP). There are different ways of generating the electricity from the scrubbed gas – via steam turbine, gas engine and, maybe some time in the future, hydrogen fuel cells.

• Highly Efficient – On an hourly basis, the PGE PRIMA 3000 is capable of generating 3 MW of electrical energy and 6 MW of thermal energy from 3 tonnes of waste. The electrical efficiency of the plant as a whole is very attractive and overall efficiency (electrical and thermal) even reaches values comparable to combined heat and power (CHP). The syngas produced is suitable for utilisation on many gas engine ranges which convert the chemical energy in the syngas into electrical energy and waste engine heat that can be recovered for drying or district heating purposes.

Potential Beneficiaries of PGE Pyrolysis Technology
• High Energy Consumption Industries – Significant energy cost savings can be achieved by utilising PGE’s pyrolysis technology to generate the energy required from waste. Employing the technology can also achieve secondary benefits including the generation of lower CO2 emissions and enhanced fuel feedstock sustainability.
Feedstock should be pre-treated to ensure that recyclable material and inert substances are removed prior to thermal processing. Subsequently it will need to be shredded to the required particle size and dried to the optimum moisture content. The surplus waste heat from the gas engine or even the pyrolysis system will be sufficient to dry the feedstock through a rotary drum or double pass dryer. Once dried it can then be stored as a Solid Recovered Fuel (SRF) in either silos or baled and wrapped for ease of stacking and inventory control.

System guarantee parameters encompass the following elements:• Gas Volume & Gas CV• Electrical Energy (Based on engine connectivity and efficiency)• Thermal Energyo Waste heat recovered from muffle furnaceo Waste heat recovered from engine exhausto Waste heat recovered from system radiators• Waste water discharge from gas scrubber system (Input to Thermal Oxidiser)• Emissions to the atmosphere• Solid residue• Parasitic loadThe system guarantee points are, in essence, determined by and subject to the received fuel quality as provided by the client. Assuming fuel quality is received according to our fuel specification, as previously outlined in this document, then the guarantee points for one tonne of Solid Recovered Fuel (SRF) are as follows:


Financial Analysis based upon System Guarantee parameters

